We have developed our own solutions to answer the problematic of design of marine propellers. The first motivation was to develop our own propeller turbines to make electricity on single-handed racing sailing boats, for Vendee-Globe competition.
1/ Lifting Line design code : running such code is our first step when creating a new propeller. Written in Julia / Python and based on various PhD Thesis and the OpenProp approach [ Brenden Epps and Richard Kimball (2013) ] it takes the input parameters and outputs a geometric table of the desired propeller.
We have developed a very specific knowledge brick to manage the case of the hydrogeneration case : that is the optimization of propeller for energy harvesting versus its drag.
This theory is however versatile and can handle the more common propulsion case where the Thrust is specified and the Torque has to be minimized, or Kaplan propellers in forced stream.
With changing the fluid parameters, we were even able to design efficient propellers for other fields of application, for example for small-scale wind-turbine.
It outputs a description of the geometry of the desired propeller as a discrete table, but is not compatible as it with CAD tools and manufacturing process.
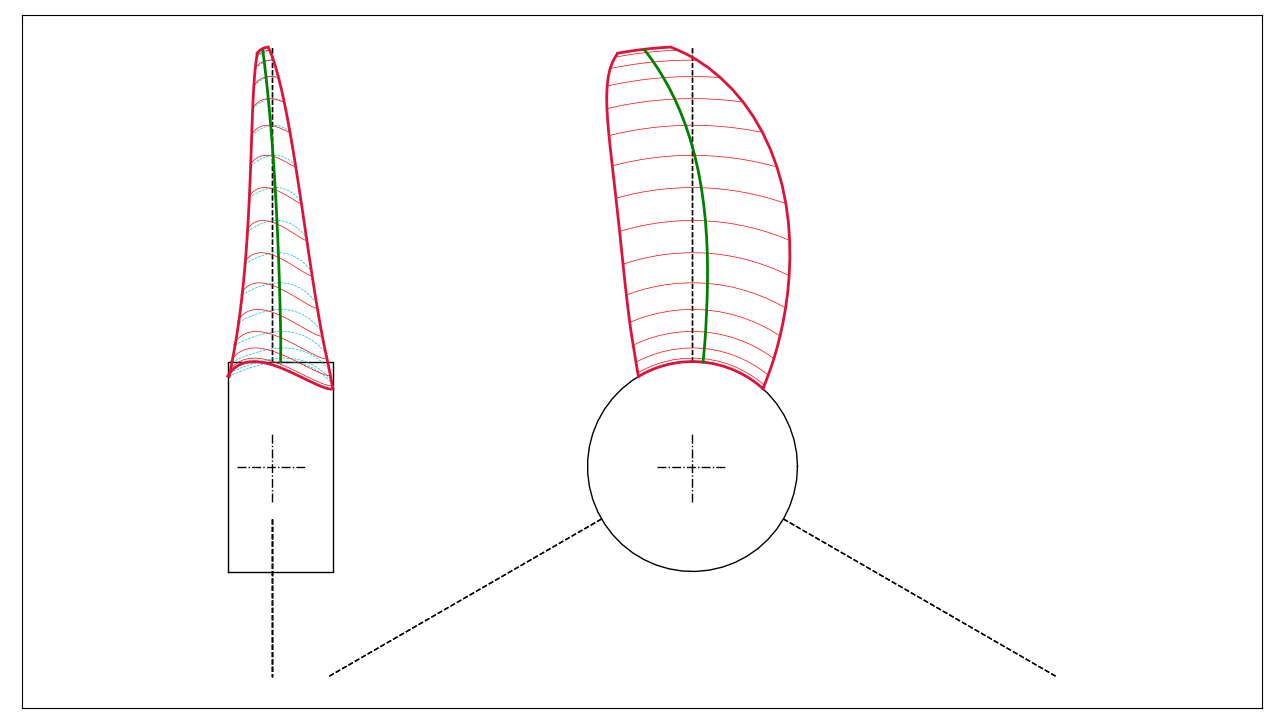
2/ 3D geometry generation : the second step to create the propeller is to “translate” the geometry table into a CAD shape. Based on a work to redefine the NACA sections into modern NURBS definitions, we are able to generate smooth and CAD-friendly shapes with good curvature continuity. This revealed mandatory to be able to alter the final shape ( e.g. to add fillets at the root ) in a robust way and allow automated CFD optimization.
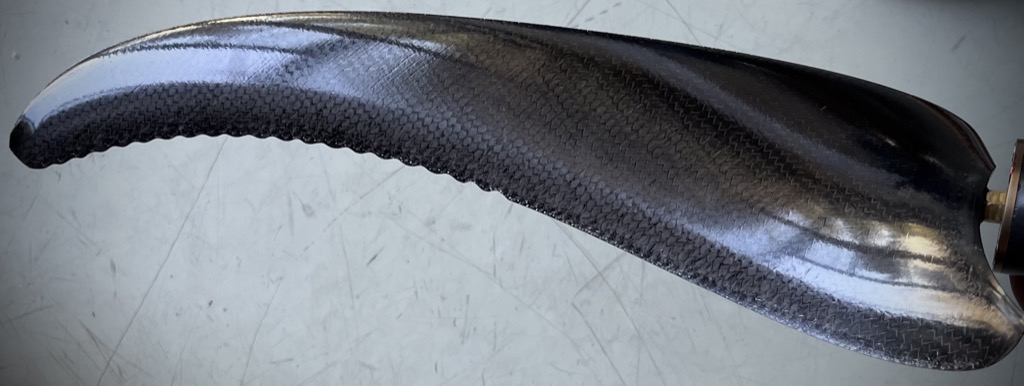
3/ CFD validation : we have developed a specific workflow with OpenFOAM solver to compute any propeller shape in open-water conditions. Some of our propellers have been tested in towing tanks allowing to check the accuracy of design and computations.
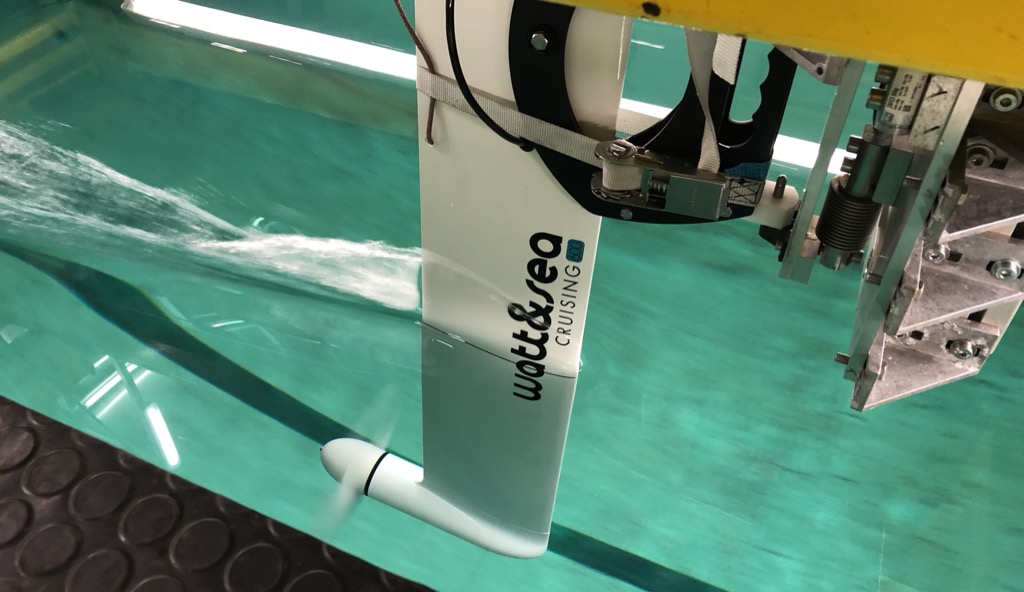
4/ CFD optimization : we are able to run optimization sets on specific parameters to maximize the efficiency and account 3D flow effects
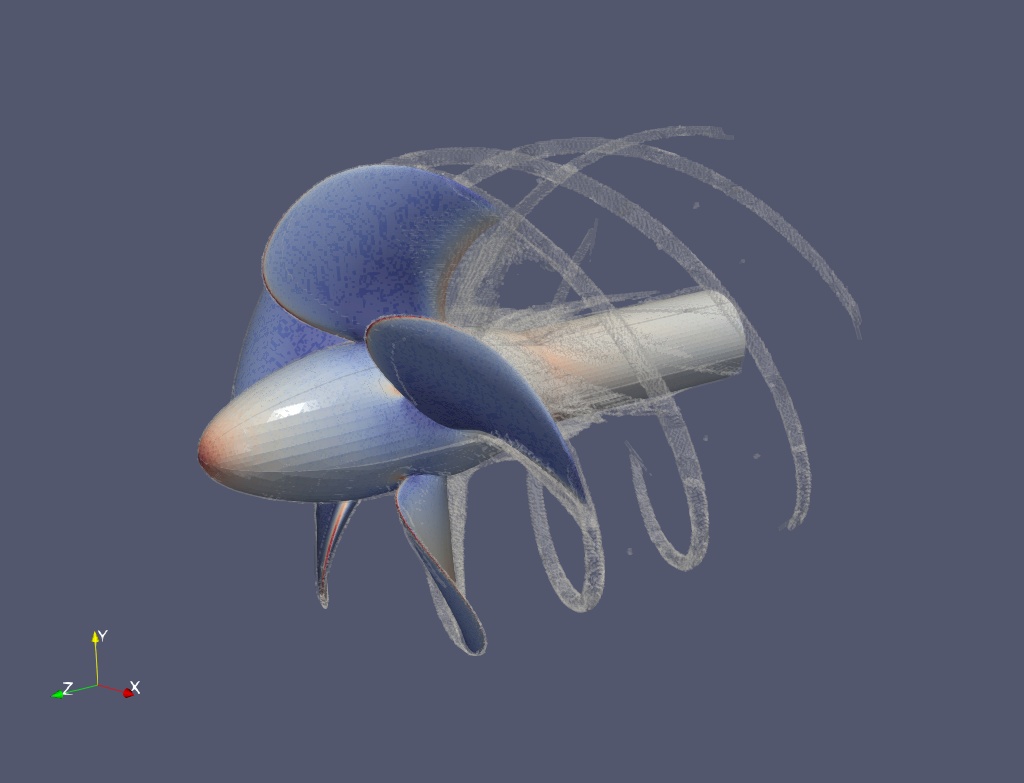
5/ Global optimization : propellers are not intended to work alone and not always at the same operating point. That’s why we have developped skills to run global optimization processes. Including motor / generator efficiency map, or usage scenarii, we are able to design a propeller that will outperform globally on its use, not only for a specific case.